Manufacturing and Analytical Services
ISSUE NO. 22 — Nanomilling for Better Solubility and Improved Bioavailability
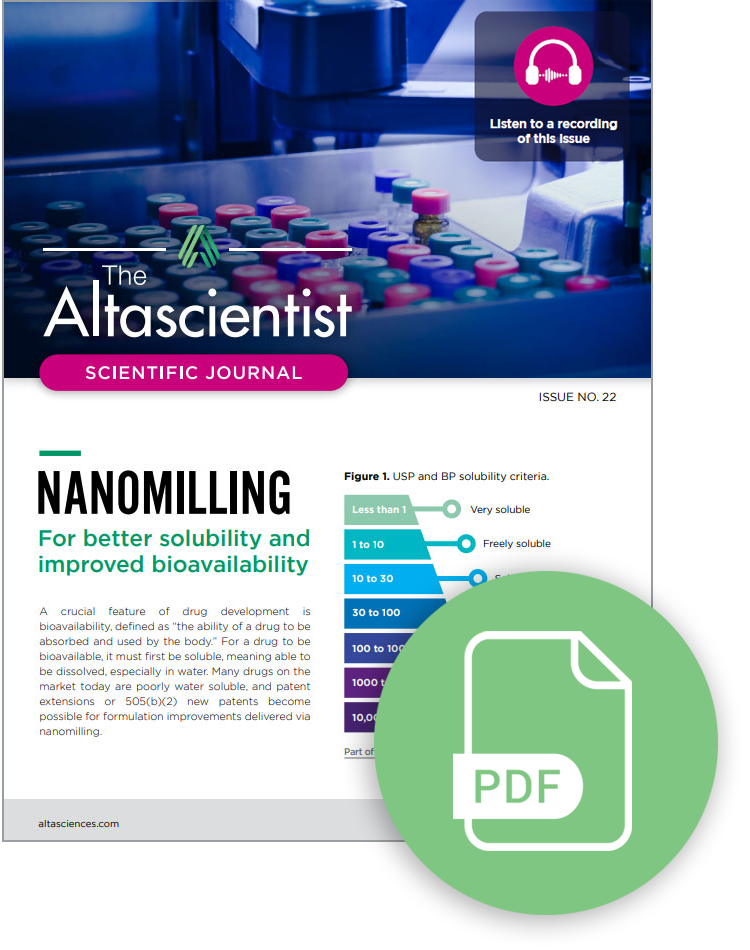
A crucial feature of drug development is bioavailability, defined as “the ability of a drug to be absorbed and used by the body.” For a drug to be bioavailable, it must first be soluble, meaning able to be dissolved, especially in water. Many drugs on the market today are poorly water soluble, and patent extensions or 505(b)(2) new patents become possible for formulation improvements delivered via nanomilling.
In Issue 22 of The Altascientist, we review:
- solubility classifications
- overcoming solubility challenges
- the benefits of nanomilling
- how nanomilling works
- maximizing formulation
Case study included!
Overcoming Solubility Challenges With Nanomilling
Promising therapeutic molecules, even if classified as poorly soluble, can be developed successfully. There are multiple technologies available to increase the solubility and oral bioavailability of poorly soluble molecules being developed as active pharmaceutical ingredients (APIs) by reducing their particle size.
Nanomilling is a universal technique that can be applied to almost any API with water solubility below 200 μg/mL. It is a very adaptable drug delivery platform suitable for oral, injectable, inhalable, and buccal applications, for which fine drug particulates are especially desired in formulations.
Nanomilling is a unit operation where mechanical energy is applied to physically break down coarse particles to finer ones. It has wide commercial and industrial applications, as every drug can be ground to finer particles, whether aqueous or non-aqueous soluble. Decreasing the size of the API molecule increases the size of the specific surface area; the larger surface area allows for greater contact with water, increasing the API’s dissolution rate and bioavailability.
The Benefits of Nanomilling
Benefits of particle size reduction for the parenteral route include small dose volumes (resulting from high drug loading) and avoidance of harsh solvents and/or extreme pH conditions. Advantages for the pulmonary route include the ability to use inhalers intended for solutions, as well as the ability to produce spray-dried powders whose particle sizes are optimized for deep lung delivery.
Other advantages include reduced fed/fasted variability in both liquid and solid dosage forms, faster onset of therapeutic action, low excipient side effects, and the ability to run continuously.
How Altasciences Can Help Improve Your Drug’s Bioavailability With Nanomilling
Nanomilling is a highly complex process requiring a unique level of CDMO expertise that can only be gained through extensive experience with developing a broad range of APIs.
At Altasciences, we can take your API from formulation to commercialization. We have the necessary procedures, equipment, and experience to work with any formulation. Our highly skilled teams work with the latest equipment, including the NETZSCH DeltaVita® 15-300 mill, that with our wet milling options can reduce particles to nanometer size, fill vials in a range of sizes (from 0.3 ml to 500 ml), and package them.
Explore all issues of The Altascientist in our Resource Center. And don’t forget to subscribe to “The Altascientist: Audiobooks” on Spotify, Apple Podcasts, or wherever you get your audio content.
Download publicationBenefits of Liquid-Filled Capsules in Pharmaceutical Development
Five Things You Need to Know About Partnering with an Integrated CRO/CDMO
We are often asked about the advantages of working with an integrated CRO/CDMO.
2021 Year in Review
![]() |
In 2021, you did incredible things — and we are grateful to have been part of your journey. ISSUE NO. 21 — Terminal Sterilization of Pharmaceutical Products
Download publication
![]() In the human health field, injectable medications, ophthalmic preparations, irrigation fluids, dialysis solutions, sutures and ligatures, implants, and certain surgical dressings, as well as the instruments necessary for their use or administration, must be presented in a sterile condition. USP <797> states: “Medications that are required to be sterile include those administered through injection, intravenous infusion (IV), intraocular (injection in the eye) or intrathecal (injection in the spine).” There is a growing demand for sterilization of small-molecule parenteral products, including heart medications, eye drops, analgesics, and antibiotics, as well as common intravenous solutions such as glucose, potassium, and saline. Many such products are used by medical professionals in hospitals, and to ensure patient safety, the drug products and related instruments and materials are sterilized at manufacture. This ensures there are no microbial contaminants like fungi or bacteria present when the product is used. In Issue 21 of The Altascientist, we review:
Terminal Versus Aseptic Sterilization for Pharmaceutical ProductsGenerally, regulatory agencies such as the FDA, EMA, among others, prefer terminal sterilization over aseptic, as it provides a high level of sterility assurance. With terminal sterilization, most drug products are produced by mixing the ingredients to form the bulk drug product solution. The bulk product is filled into a tightly sealed container and the entire container is sterilized. Terminal sterilization also offers time savings and cost advantages to pharmaceutical companies. Since terminal sterilization takes place after the formulation and filling steps, these initial manufacturing processes can occur in a less rigidly structured environment, which lowers the complexity, increases the speed, and therefore positively impacts the cost of manufacturing. When terminal sterilization is not an option, aseptic processing is used. Each component (drug, container, closure, etc.) is individually sterilized first, then carefully assembled in a dedicated clean room with a highly controlled environment to make the finished drug product in a manner that prevents contamination. Containers, closures, and filling materials go through their own validated sterilization cycles. Aseptic processing cannot provide the same quantitative level of sterility assurance as terminal sterilization, but it features several layers of control to minimize the risk of contamination. Why Terminal Sterilization is the Ideal Choice for Pharmaceutical ProductsTerminal sterilization is the preferred method for drug products because sterilization takes place after the product has been filled into the primary packaging, thus severely limiting further opportunities for contamination due to human intervention. The process is reliable, repeatable, and delivers an excellent quality product. Terminal sterilization is also less complex, less costly, and more easily reproducible than aseptic processing. When conducted by well-trained, knowledgeable experts, sterilization conditions can be adapted to ensure they are appropriate to the drug product in question, and deliver the robust, thorough sterility results expected from this type of process. In Altasciences’ Grade C suites, we develop injectable drug products and topical ophthalmic preparations that can be terminally sterilized after manufacture. All such drug processing is conducted in our Grade C, cGMP facility, which has been inspected by both the FDA and the European Union Quality Personnel. Our team will guide you in the selection, method development and validation, and final delivery of fully sterilized product. We have decades of experience as a CDMO, and will ensure the efficient, effective implementation of the most appropriate sterilization method for your drug products.
Explore all issues of The Altascientist in our Resource Center. And don’t forget to subscribe to “The Altascientist: Audiobooks” on Spotify, Apple Podcasts, or wherever you get your audio content. Psychedelics — Regulatory Environment Challenges
.custom-column-left-text {
float: left;
width: 50%;
padding-right: 10px;
}
.custom-column-right-text {
float: right;
width: 45%;
text-align:center;
}
@media only screen and (max-width: 600px) {
.custom-column-left-text,
.custom-column-right-text,
.custom-column-flc-ebook-text {
float:none;
width:80%;
margin:0 auto;
}
}
A History of Public Attitude Towards Psychedelic DrugsPsychedelic drugs exist within a unique social, legal, and historical environment, with roots in the public imag Five Ways Altasciences Simplifies the Drug Development Process for You
.custom-column-left-text {
float: left;
width: 50%;
padding-right: 10px;
}
.custom-column-right-text {
float: right;
width: 45%;
text-align:center;
}
@media only screen and (max-width: 600px) {
.custom-column-left-text,
.custom-column-right-text,
.custom-column-flc-ebook-text {
float:none;
width:80%;
margin:0 auto;
}
}
Bringing new drugs to market, from lead candidate selection through preclinical testing, to clinical proof of concept, is a complex, time-consuming, and costly process. Making Early-Phase Drug Development Faster, Better, and More Efficient
.custom-column-left-text {
float: left;
width: 50%;
padding-right: 10px;
}
.custom-column-right-text {
float: right;
width: 45%;
text-align:center;
}
@media only screen and (max-width: 600px) {
.custom-column-left-text,
.custom-column-right-text,
.custom-column-flc-ebook-text {
float:none;
width:80%;
margin:0 auto;
}
}
Early-phase drug discovery and drug development are complex processes, where many moving parts can, and do, influence the success of a program. Applications of Liquid-Filled Capsules for Challenging APIs in Pharmaceutical Manufacturing
Nanomilling from Screening to Scale-up
|